解读丰田生产模式(三)
发布时间:
2020-12-02
来源:
本文分四期连载,共同分享丰田公司先进的生产管理模式。
(接上期)
3、作业流程分类
TPS将作业流程分为以下三类:一类是可以提高产品附加价值的作业。如生产作业中的安装零部件、压铁板、焊接;物流作业中的存放作业、提取作业、包装作业等。第二类是虽然无附加价值,但在现有工作条件下是必要的程序。如生产作业加的提取零部件作业、分步作业;物流作业中的搬运空装载板,定期地进行整理,分开进货等。第三类便是工作上本来不必要的程序。如生产作业、物流作业中的无业务(需要等待从前一个过程传过来的产品),寻找产品(由于产品未放在固定的位置而需要寻找),以及生产作业中的次品加工等。其中第三类便是TPS需要尽力发现并彻底排除的不必要流程。
4、TPS的7个不必要的流程
TPS总结出了以下7种比较典型的不必要流程。
①过量生产的不必要流程。过量生产的不必要流程被丰田公司认定为最不必要的流程,下一节我们将详细介绍。
5、过量生产—丰田最不必要的流程
造成企业过量生产的原因是多方面的,但就生产而言,主要有以下两点;一是企业生产能力过剩,具有多余的职工和设备,有能力进行过量生产;二是企业为了保障对设备发生故障或发生次品等万一事情时的产品需求,从而需要一部分过量生产以备不时之需。
过量生产是TPS认定的最不必要的流程。它造成了企业资源的巨大浪费,同时又导致了另一些不必要的流程。如:
①没法发现无业务(不必要的余力);
②过剩的库存(不必要的库存);
③增加设备(不必要的投资);
④需要建仓库(不必要的投资和空间占用);
⑤仓库的搬运工作(不必要的搬运);
⑥发生搬运时的损坏(不必要的再加工);
⑦因为不能出货而使产品过时导致产品的处理再加工(不必要的再加工);
⑧需要管理库存的职工(不必要的人工费);等等。
此外,一个不必要导致另一个不必要的发现,结果不知道是哪一个流程是不必要的,使得无法发现问题,看清问题,不知道应该从哪里着手解决问题。
6、排除不必要的流程,提高效率
TPS认为,提高效率和强化劳动是两个不同的概念,不进行改善而强迫职工工作,加大工作强度,如提高工作速度、强迫重作业、强迫不安全作业,以此方式来提高效率是行不通的。TPS提高效率的主要方式便是尽力排除不必要的流程,把“不必要的动作”变成“有效的动作”,使职工专心于有价值的作业。
(待续...)
下一页
下一页
相关新闻
联系方式
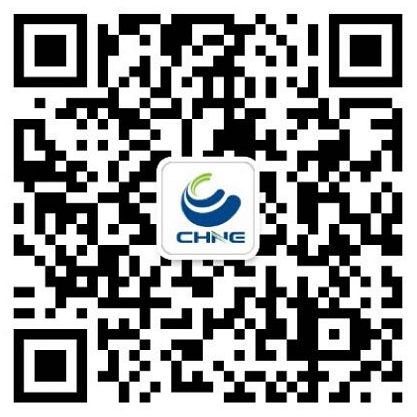
微信公众号
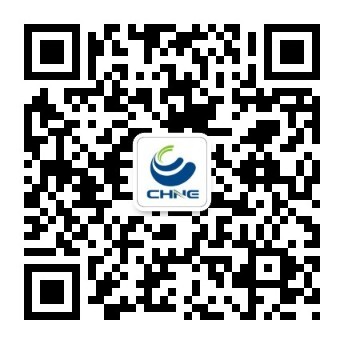
微信订阅号